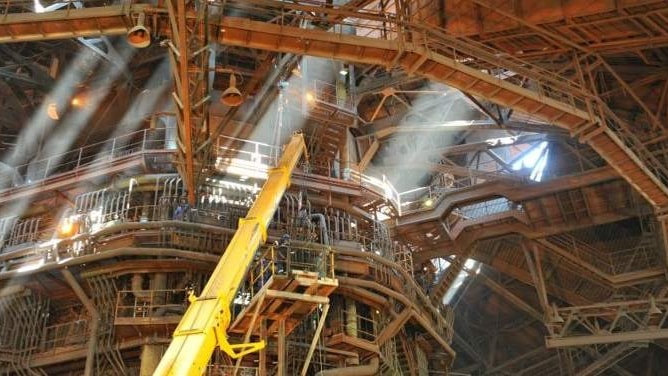
Waste not, want not – forging a modern heat recovery system
E.ON and ArcelorMittal forge a cutting-edge heat recovery system
Making steel is hot work – in the case of Poland’s largest steel manufacturer that sometimes means 1,200 degrees of it! In a pioneering collaboration, E.ON and ArcelorMittal have joined forces to introduce a cutting-edge heat recovery system that will capture otherwise waste energy and return it to the production processes – yielding significant energy savings, reducing emissions and improving security of supply in the steel-making process.
This innovative technology is now in operation and will play a crucial role in reducing CO2 emissions from the blast furnace in the city of Dąbrowa Górnicza.
At the core of the facility, heat exchangers capture heat from flue gases reaching up to 250°C and recycle that energy back into the production process, marking a revolutionary leap towards more sustainable steel production with significant results:
- 56,000 tonnes reduction in CO2 emissions each year
- 117 GWh of energy recovered each year – equivalent to the gas consumption of more than 10,000 UK homes
- A significant decrease of almost 10,000 tonnes in coke fuel consumption
The heat recovery system is the result of many years of cooperation between E.ON and ArcelorMittal, supporting its targets to reduce carbon emissions across Europe by 35% until 2030. This latest project is one of the many ways E.ON supports heavy industry with efficiency and environmental aims.
In the UK E.ON has forged an agreement with Sheffield stainless steel manufacturer Marcegaglia that will recover and distribute waste heat from the melting process into E.ON’s district heating network in the Lower Don Valley. Once operational, this will play a key role in enhancing the resilience of the region’s energy infrastructure and contribute to Sheffield City Council’s wider decarbonisation goals.